La creazione, o la modernizzazione, di una smart factory costituisce una delle sfide più importanti per il settore manifatturiero. Senza esagerazioni, la potremmo definire la sfida del secolo dal momento che le potenziali ricadute sono paragonabili solo a quelle dell’adozione dell’automazione nel secolo scorso. L’obiettivo di una smart factory è quello di diventare un sistema flessibile, completamente connesso e in grado di fornire, e appoggiarsi a, un flusso di dati costante e affidabile.
Grazie alla connettività e all’uso dei dati in tempo reale, la fabbrica intelligente è in grado di adattarsi alle richieste del mercato, alle condizioni contingenti, ottimizzarsi in modo automatico e adottare processi di auto apprendimento per conservare prestazioni e competitività.
Smart Factory: la definizione canonica
Secondo la definizione di Gartner la fabbrica intelligente è un concetto usato per descrivere l’applicazione di moderne tecnologie per creare una capacità di produzione iper-flessibile e auto adattante. Parlando di Smart Factory, una definizione è già comparsa sulle nostre pagine, in cui abbiamo posto un particolare accento anche sul fattore umano: considerare l’automazione prima e la smart factory poi come concetti in competizione con la valorizzazione del personale e dei tecnici, infatti, è un errore piuttosto comune. In questo approfondimento, invece, andremo a concentrarci principalmente sugli aspetti tecnici che costituiscono, a livello di principio, i requisiti necessari per avviare un processo di implementazione, o di trasformazione, della fabbrica intelligente.
I requisiti basilari della smart factory
Parlando di Smart Factory, il significato da attribuire ai requisiti è, naturalmente, piuttosto generico: l’implementazione nel mondo reale è complessa e articolata ma, come sempre, partire dai principi fondanti permette di cogliere meglio la visione di insieme e prendere decisioni strategiche. Potremmo in qualche modo definirli principi di progettazione, che devono essere seguiti sia per la costruzione di nuovi impianti e stabilimenti, sia per la modernizzazione di quelli esistenti.
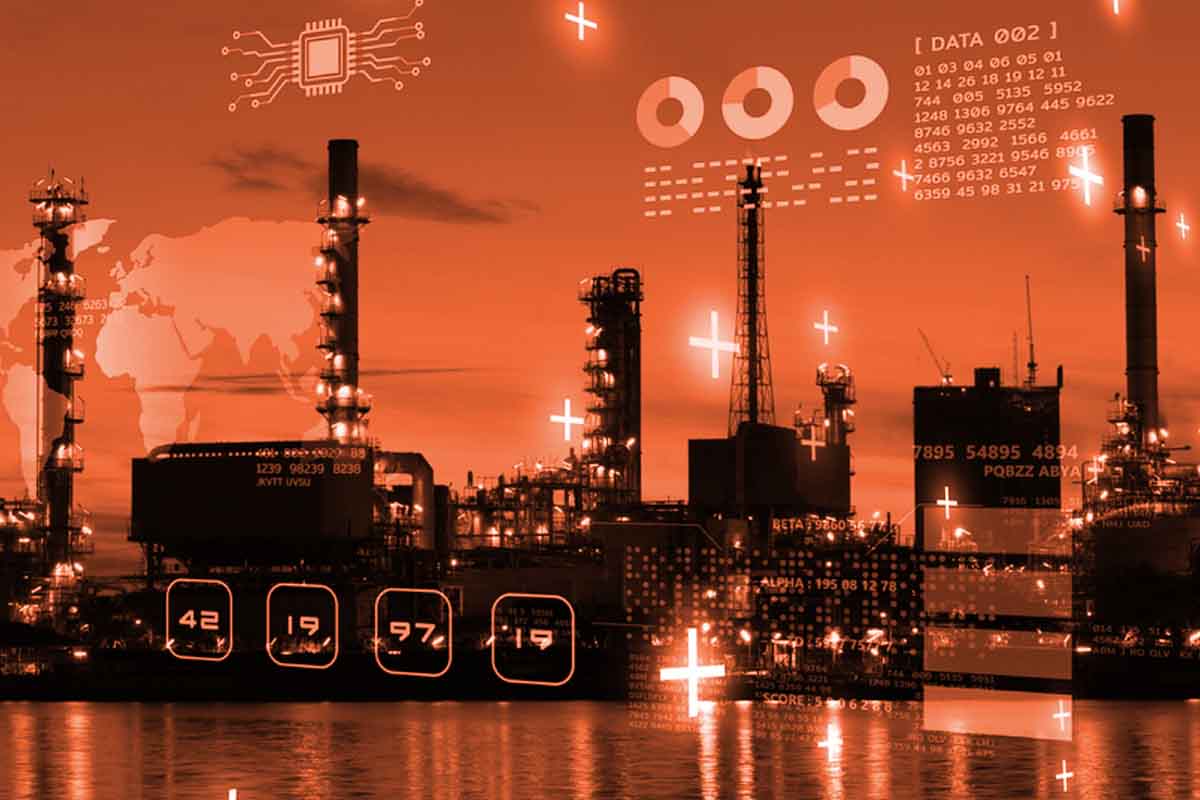
- La modularità si riferisce alla capacità dei componenti di un sistema (in questo caso l’impianto o lo stabilimento) di essere separati e combinati rapidamente, possibilmente in tempo reale e senza bisogno di fermi prolungati. In questo modo i sistemi possono rispondere alle richieste esterne o interne rapidamente. La modularità permette anche di rispondere in modo efficiente a eventuali malfunzionamenti e di integrare nuovi moduli o funzionalità in modo agile.
- L’interoperabilità si inserisce in un contesto più ampio che, come sappiamo, è uno dei principi fondanti anche di Industria 4.0: dati e informazioni devono essere permeabili e poter essere raggiunti, ed elaborati, in tempo reale da tutti i sistemi di controllo e gestione. L’interoperabilità è il primo tassello per raggiungere questo obiettivo: sistemi e macchinari devono poter trasferire informazioni lungo tutta la filiera.
- La capacità di risposta in tempo reale è un altro elemento fondamentale. Un sistema, in questo caso un impianto o uno stabilimento, deve poter rispondere il più rapidamente possibile a variazioni e sollecitazioni.
- La decentralizzazione è un altro elemento fondamentale. Le diverse parti che costituiscono il sistema, per esempio la logistica, ma anche i singoli moduli di produzione e i macchinari, devono essere in grado di gestire decisioni in modo autonomo, in tempo reale e in modo non subordinato a una decisione centralizzata, in modo da non rallentare le operazioni. Naturalmente le decisioni autonome devono essere armonizzate in modo da non contravvenire agli obiettivi dell’azienda. In parole più semplici, ogni unità deve poter operare anche in modo autonomo.
- Infine, la virtualizzazione è un altro aspetto che deve essere preso in considerazione. La creazione di un ambiente virtuale che replichi lo stabilimento reale, come suggerisce per esempio la tecnica del digital twin, offre la possibilità di monitorare e simulare i processi reali. Questo sistema permette anche, per esempio, di effettuare un collaudo almeno di primo livello su prototipi e processi produttivi, contenendo costi e tempi.
Creare una fabbrica intelligente e pronta a raccogliere le sfide
Abbiamo visto quali sono i principi fondamentali su cui si dovrebbe basare un progetto di smart factory; tuttavia, è bene porre l’accento anche su un concetto più soft ma altrettanto importante, ovvero l’armonizzazione delle risorse e delle soluzioni. Concetti come permeabilità dei dati, interoperabilità e capacità di risposta infatti possono trovare reale applicazione solo se accompagnati da una visione condivisa e a una conseguente gestione del cambiamento. Innovazioni così rivoluzionarie, infatti, devono essere accolte prima di tutto dal management, e trasmesse correttamente a tutte le persone, per essere accolte nel modo migliore.
In Regesta LAB ti supportiamo durante tutto il percorso di trasformazione digitale, aiutando la tua azienda a diventare un’impresa intelligente. Contattaci per ricevere informazioni.