La transizione verso il digital manufacturing rappresenta oggi un’opportunità concreta per la maggior parte delle realtà manifatturiere. La rivoluzione introdotta da Industria 4.0 ha profondamente modificato l’approccio delle fabbriche alla gestione dei processi, privilegiando sistemi interconnessi e interattivi. L’introduzione delle cosiddette “tecnologie abilitanti” ha tracciato un percorso che, nonostante alcune iniziali resistenze, ha contribuito significativamente a migliorare il rapporto tra le aziende e l’innovazione digitale.
In questo nuovo paradigma produttivo, la capacità di acquisire e analizzare i dati in tempo reale emerge come elemento cruciale, garantendo una connessione funzionale tra le diverse fasi del processo produttivo e facilitando una comunicazione organizzativa efficace.
La digitalizzazione documentale degli archivi cartacei: una necessità per l’efficienza aziendale
Molte aziende sono ancora sommerse da archivi cartacei. Questi documenti occupano spazio, costano in termini di gestione e richiedono tempo per essere consultati. Ma, soprattutto, all’interno di questo mondo analogico si nasconde spesso un vero patrimonio di conoscenza aziendale che rischia di andare perduto. La soluzione, fortunatamente, è a portata di mano. Il primo passo è la digitalizzazione degli archivi cartacei. Trasformare fogli fisici in documenti digitali significa rendere tutto più accessibile e veloce.
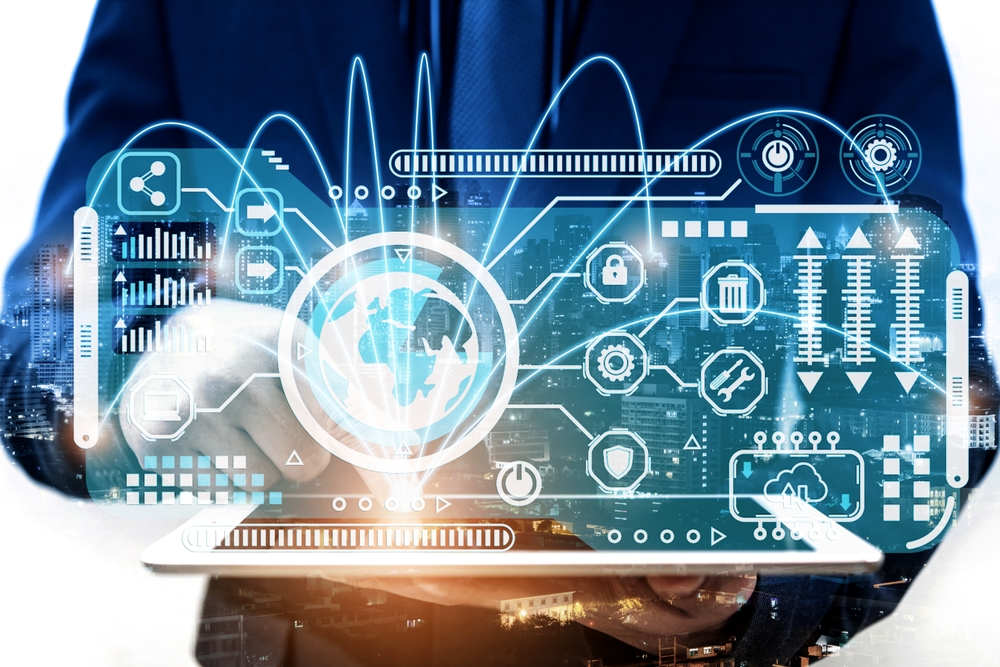
La fabbrica connessa e il valore della real time data analysis
L’utilizzo dei dati in tempo reale negli ambienti produttivi connessi ha assunto un’importanza strategica universalmente riconosciuta. Questo approccio consente alle aziende di adottare decisioni basate sui dati (data driven), tempestive e informate, con evidenti benefici in termini di agilità operativa, efficienza e riduzione degli sprechi. L’analisi in tempo reale si rivela particolarmente preziosa nel monitoraggio delle prestazioni dei macchinari, nella previsione di eventuali guasti e nell’ottimizzazione della produzione in base a condizioni contingenti che gli strumenti tradizionali, sia analogici sia digitali non real-time, non sarebbero in grado di rilevare.
La rapidità nelle operazioni e nei processi decisionali rappresenta un fattore competitivo cruciale per le imprese manifatturiere. Il digital manufacturing si basa sul concetto di fabbrica connessa, dove ogni componente – dai macchinari ai sensori – è integrato in una rete capace di raccogliere, elaborare e distribuire informazioni. Tuttavia, questo modello presenta diverse sfide tecnologiche e organizzative:
- Gestione di grandi volumi di dati: la fabbrica connessa genera quantità significative di dati provenienti da dispositivi IIoT, software ERP, sensori e altre fonti. La sfida non si limita alla raccolta, ma si estende alla capacità di estrarre informazioni utili in tempo reale.
- Interoperabilità: l’integrazione di diverse tecnologie, protocolli e modelli di database richiede soluzioni capaci di creare un sistema informativo coerente e uniforme.
- Scalabilità: le infrastrutture digitali devono poter crescere parallelamente all’aumento dei dispositivi e degli impianti connessi, mantenendo prestazioni ottimali.
- Sicurezza: l’incremento dell’interconnessione e della condivisione dei dati in tempo reale richiede particolare attenzione alla cybersecurity.
Bishop: la risposta alle sfide del digital manufacturing
Per affrontare queste problematiche, Bishop si propone come soluzione integrata. Realizzato da Ultrafab, realtà recentemente entrata a far parte del Gruppo Regesta, rappresenta una piattaforma avanzata per la gestione e l’ottimizzazione dell’analisi dei dati in tempo reale nel contesto della fabbrica connessa.
Configurandosi come sistema operativo real-time, Bishop elabora i dati attraverso la Real Time Streaming Analysis, fornendo alle aziende un’infrastruttura che permette di rispondere tempestivamente agli eventi e di migliorare la reattività operativa.
Accesso ritardato ai dati critici
Una delle principali difficoltà per le aziende è l’accesso tardivo alle informazioni necessarie per prendere decisioni rapide. Questo ritardo può portare a inefficienze, sprechi o, nel peggiore dei casi, interruzioni nel flusso produttivo.
Soluzione Bishop: l’architettura orientata ai messaggi di Bishop trasforma ogni evento significativo in un messaggio con timestamp, garantendone l’elaborazione immediata e la notifica ai responsabili. Questo meccanismo assicura un monitoraggio in tempo reale e interventi tempestivi, ottimizzando i tempi di risposta e riducendo i costi operativi.
Complessità nella gestione di dati da più fonti
Nelle fabbriche connesse uno dei problemi principali è l’aggregazione di dati provenienti da fonti diverse, come sensori IIoT, software e PLC. La mancata integrazione tra questi sistemi può creare disallineamenti e ostacolare la continuità operativa.
Soluzione Bishop: il sistema eccelle nell’aggregazione di informazioni provenienti da fonti diverse distribuite su più impianti, uniformandole per una fruizione immediata. Questa capacità di dialogo con sistemi eterogenei offre una visione completa delle operazioni, facilitando l’ottimizzazione dei flussi di lavoro.
Sovraccarico informativo e difficoltà nel reporting
Con l’aumento esponenziale dei dati collezionati le aziende spesso si trovano ad affrontare un eccesso di informazioni che rende complesso distinguere gli eventi critici da quelli meno rilevanti.
Soluzione Bishop: per contrastare il sovraccarico informativo, la piattaforma implementa un sistema di notifiche mirate per gli eventi rilevanti, razionalizzando il processo di reporting e permettendo alle aziende di concentrarsi sulle informazioni essenziali.
Gestione distribuita e scalabilità
Con la crescente complessità delle operazioni, anche in senso territoriale, è necessario essere in grado di monitorare in tempo reale più impianti dislocati in paesi diversi, e di conservare anche in questo caso un accesso tempestivo ai dati.
Soluzione Bishop: l’architettura scalabile di Bishop consente il monitoraggio in tempo reale di impianti dislocati in diverse aree geografiche, mantenendo una visione centralizzata e un controllo operativo efficace indipendentemente dalla localizzazione.
Connessione dei dati e comunicazione di informazioni: vincere la sfida con Bishop
L’adozione di una soluzione come Bishop, con le sue capacità di analisi in tempo reale e gestione integrata dei dati, rappresenta una risposta concreta alle esigenze del digital manufacturing contemporaneo. In un ambiente industriale sempre più connesso, la capacità di analizzare i dati in tempo reale permette alle aziende di ottimizzare l’efficienza, contenere i costi e anticipare le criticità, garantendo un vantaggio competitivo sostenibile nel tempo.
Contattaci e scopri come Bishop può accelerare il percorso digitale della tua azienda!