Il vecchio approccio alla produzione era frammentato. Ogni reparto aveva il proprio software, i propri dati, e il proprio modo di gestirli, dando luogo a un problema di frammentazione ben noto. In alcuni casi la trasformazione richiesta dall’industria 4.0 ha mitigato questo problema, ma non lo ha risolto del tutto. Con ogni parte dell’azienda su un percorso separato, avere una visione coesa delle prestazioni dell’azienda è sempre stato complesso. Le lacune nella comunicazione, i colli di bottiglia e in generale i problemi dovuti alla compartimentazione sono ancora oggi il principale freno alla trasformazione delle aziende manifatturiere in Smart Factory, e alla progressiva perdita di competitività.
Nel corso degli anni, la tecnologia ha fatto molta strada per aumentare la connettività aziendale. Il cloud computing e l’accessibilità universale consentono ai produttori di avere una visione di insieme in ogni momento. Gli ERP sono diventati la spina dorsale della produzione, aggregando i dati e rendendoli immediatamente disponibili, ma soprattutto consentendo livelli di analisi avanzata impossibili in un sistema non integrato.
I vantaggi dell’Industria 4.0 sono noti già da tempo: secondo un rapporto di McKinsey del 2017 l’innovazione ha portato una riduzione del 30-50% dei tempi di inattività e un aumento del 40-50% della produttività del lavoro. L’adozione di un ERP nell’industria 4.0 è la naturale evoluzione di questo processo, per raggiungere lo status di Smart Factory, che a oggi costituisce il punto più alto della competitività tecnologica.
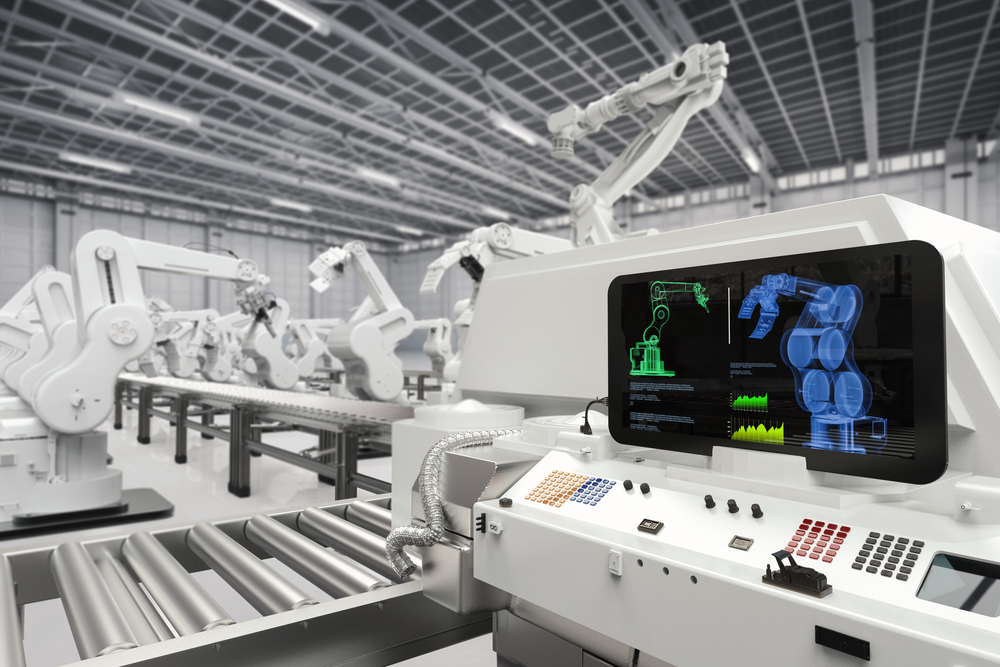
ERP e Industria 4.0: i principali ambiti di miglioramento
Il primo aspetto che va sottolineato è che per molti versi il passaggio da industria 4.0 a smart factory non è disruptive come gli altri passaggi della trasformazione digitale. Anzi, in molti casi ne è la naturale evoluzione. Vediamo ora in quali contesti la maggiore integrazione di un ERP nei processi aziendali può portare benefici
consistenti, armonizzando le comunicazioni e permettendo una analisi dei dati più puntuale ed efficiente.
Efficientamento dei cicli produttivi
Colli di bottiglia inutili come prodotti che non soddisfano la qualità attesa dai clienti, ritardi nella produzione a causa di guasti alle macchine o materie prime inadeguate, possono sorgere a causa della mancanza di informazioni e dati adeguati, o di qualsiasi non idealità nel processo produttivo. L’inefficienza dei cicli produttivi incide molto sui profitti.
Un ERP come SAP S/4HANA permette il monitoraggio, per esempio, dei tempi per ogni ciclo, il tempo di produzione per singolo prodotto e il coordinamento dei task necessari, per identificare inefficienze e potenziali criticità.
Riduzione dei fermi di produzione
I prodotti possono essere consegnati ai clienti nelle tempistiche concordate se e solo se ogni macchinario funziona alla perfezione. Guasti improvvisi, problemi di approvvigionamento e altre inefficienze possono minare la fluidità del processo produttivo.
Un ERP dotato per esempio di un sistema di manutenzione predittiva e di un monitoraggio dell’intera catena di produzione può identificare in modo efficace eventuali criticità e contribuire alla prevenzione.
Bilanciamento dei flussi di lavoro
Colli di bottiglia e problemi legati all’efficienza possono verificarsi in una linea di produzione quando una postazione è sovrautilizzata o sottoutilizzata. Se il bilanciamento del carico di lavoro richiede un intervento manuale nell’assegnazione dei task e nella temporizzazione, questo può introdurre inefficienze.
Una soluzione ERP offre il vantaggio di monitorare il tempo medio necessario per eseguire un lavoro sulla linea di produzione. Di conseguenza, i supervisori possono avere stime di tempo più precise per bilanciare adeguatamente la linea di produzione. Nelle soluzioni più avanzate è possibile che questo bilanciamento
avvenga in modo automatico.
Accesso alle informazioni in tempo reale
In alcuni casi le aziende non dispongono di infrastrutture adeguate o di strumenti in grado di monitorare le linee di produzione in modo centralizzato. Questo può comportare un ritardo nel trasferimento delle informazioni alle rispettive autorità.
Un ERP è puo creare un ambiente di fabbrica sensibile al contesto, in grado di tracciare e monitorare in tempo reale le attività critiche nella produzione utilizzando un sistema di comunicazione decentralizzata per una gestione ottimale dei processi di produzione.
I passaggi pratici per l’adozione globale di un ERP nell’industria 4.0
La transizione verso la smart factory nel manufacturing incontra tutte le criticità tipiche dei sistemi che fanno dell’efficienza produttiva una risorsa fondamentale. Anche se i benefici sono considerevoli infatti, non sempre è possibile effettuare tutti gli aggiornamenti necessari nel breve o medio periodo, proprio perché questo potrebbe costringere a fermi di produzione prolungati.
La cosa migliore da fare in questi casi è creare, insieme agli specialisti, un piano a medio (o lungo) termine che permetta un passaggio il più possibile trasparente e, dove necessario, un adeguamento o un cambiamento dei macchinari.
Prima di tutto è necessario censire con precisione gli asset, in modo da identificare le risorse più obsolete che potrebbero essere bloccanti per il processo.
Nella prima fase è necessario identificare i singoli blocchi costitutivi dell’architettura. Per esempio, se i macchinari dispongono di sistemi di monitoraggio e di che tipo, e soprattutto identificare le strategie per passare da un contesto di sistemi isolati a uno di sistemi integrati.
Il primo passaggio fondamentale infatti è che i dati e le informazioni provenienti dai tutti i reparti, dagli ordini alla produzione, passando per gli acquisti e la logistica, per esempio, siano universalmente fruibili all’interno della struttura. Spesso per i passaggi amministrativi è sufficiente una riorganizzazione, o semplicemente l’adozione definitiva di una soluzione ERP, mentre per gli aspetti produttivi potrebbe essere necessario introdurre nuovi sistemi di monitoraggio, per esempio utilizzando soluzioni IIoT per i macchinari, oppure con il passaggio a macchinari di nuova generazione che dispongano nativamente degli strumenti necessari. In questo passaggio si provvederà anche ad armonizzare i dati, per esempio attraverso l’adozione di standard.
Il secondo passaggio è quello legato all’utilizzo dei dati per l’automazione dei processi. Una volta verificato che i dati fluiscono correttamente, è possibile sfruttare la nostra soluzione ERP per un monitoraggio in tempo reale, per l’individuazione delle criticità e in generale per tutti i miglioramenti offerti dalla possibilità di poter gestire, analizzare e verificare i dati in tempo reale, per esempio per attivare una seconda fornitura di materiali, per pianificare correttamente le spedizioni senza sovraccarichi alla logistica e così via. L’analisi dei dati in tempo reale a questo punto aprirà le porte al passaggio successivo.
Infine i dati raccolti in modo consistente e verificati permetteranno all’azienda di implementare soluzioni realmente smart, per esempio manutenzione predittiva e predictive quality analytics ma non solo. Grazie a sistemi evoluti e basati sul machine learning sarà possibile attivare sistemi predittivi avanzati, come la possibilità di utilizzare il gemello digitale per collaudare una nuova filiera produttiva prima della reale implementazione, o il coordinamento centralizzato e in tempo reale di più impianti, anche dislocati in territori molto distanti.