Qualità Predittiva e Rilevazione delle Anomalie nell’Industria dell’Acciaio
Nell’industria dell’acciaio la qualità del prodotto è uno dei migliori indicatori della stabilità del processo produttivo. Produrre con una qualità costante, prevedibile e adeguata è una delle principali ambizioni nei processi industriali. Poter prevedere quale sarà la qualità del prodotto a partire dai dati raccolti durante la sua lavorazione permette di rilevare, identificare ed eventualmente correggere le sorgenti di instabilità nella produzione. Da qui nasce l’esigenza di mettere in campo sistemi di predictive quality, qualità predittiva, per prevenire e risolvere problematiche che possano compromettere le caratteristiche del materiale.
Nel caso della manifattura dell’acciaio, infatti, le resistenze agli sforzi meccanici sono tra le variabili più significative da tenere in considerazione. Negli impianti di produzione su larga scala, effettuare test in maniera estensiva e precisa risulta dispendioso sia economicamente che temporalmente. Nell’ambito della manifattura dell’acciaio, i progetti di qualità predittiva permettono di migliorare gli aspetti legati ai test effettuati sui prodotti.
Come i modelli di Machine Learning possono aiutare a migliorare la qualità dei prodotti
Le caratteristiche chimiche della colata di acciaio e la sua storia di lavorazione sono tra le principali variabili influenzano le caratteristiche meccaniche del prodotto finito. Parallelamente, sono anche fonte di numerose informazioni che un processo di predictive quality può utilizzare per costruire un modello previsionale affidabile.
Perché un processo di qualità predittiva sia davvero efficace è necessario sfruttare queste sorgenti informative nel modo giusto.
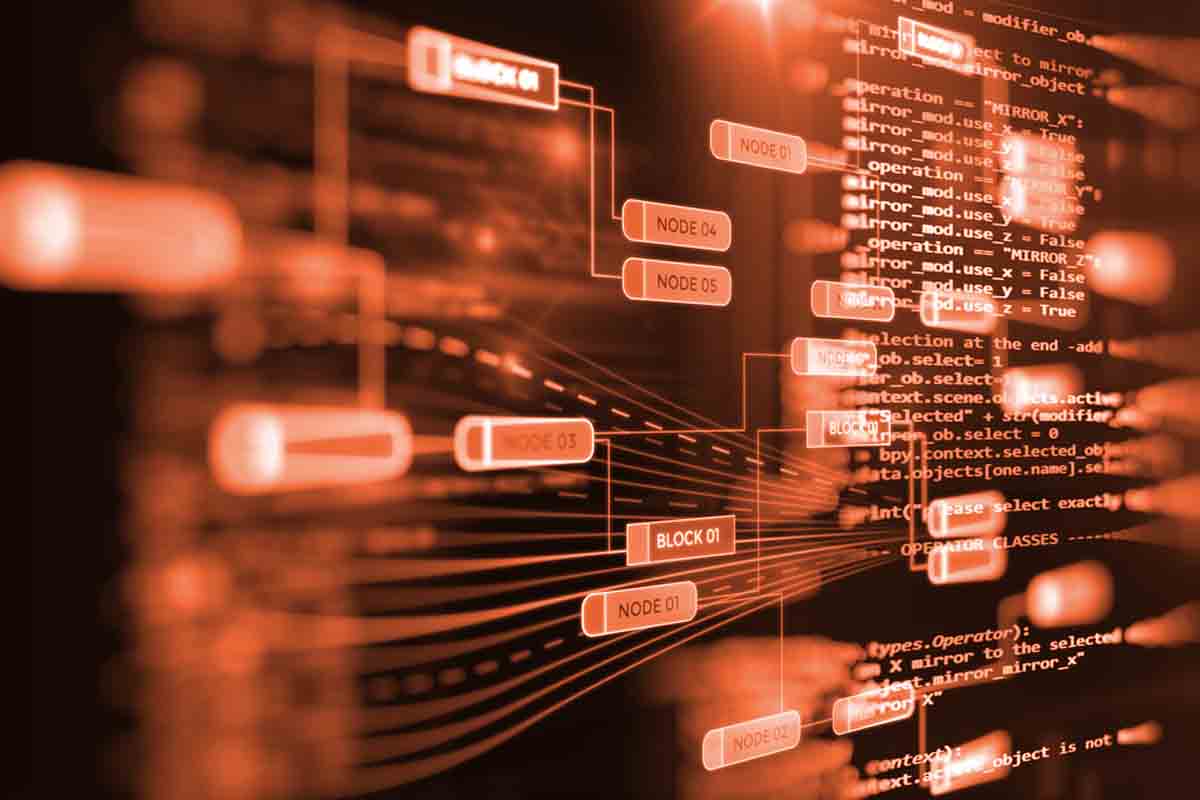
Questo richiede la gestione della grande quantità di dati generata dai sensori sugli impianti di produzione. Le sfide principali di questa fase sono le seguenti:
- accogliere e rendere disponibili i dati in tempi near-real-time: un’architettura orientata all’IoT è essenziale per convogliare i dati dei sensori verso basi di dati ad hoc che possano offrire prestazioni elevate verso i modelli di intelligenza artificiale che li dovranno interpretare.
- pulire i dati dall’incertezza strutturale presente nel processo: i processi reali sono soggetti ad una costante evoluzione nel tempo alla quale concorrono eventi di manutenzione, rinnovo o sostituzione dell’impianto assieme a quelli che sono i comportamenti imprevedibili dovuti a fattori esterni.
- selezionare le variabili più significative per la previsione della qualità: nell’immenso flusso di dati in arrivo dai sensori, solo una parte è portatrice di informazioni significative alla previsione della qualità del prodotto quindi la feature-selection è essenziale per ridurre la mole di dati senza perdita di informazioni utili.
Applicando queste buone pratiche, il flusso massiccio e disordinato si trasforma in un dataset coerente, essenziale e rilevante per essere elaborato in un’accurata modellizzazione del processo, oppure un algoritmo di apprendimento automatico addestrato sullo storico dei dati. Il modello impara a fornire in output uno (o più) indici di qualità del prodotto a partire dai dati di lavorazione raccolti lungo la catena di produzione rendendo i test più estensivi e automatizzati.
L’approccio di Regesta Lab alla predictive quality
Durante il processo di sviluppo abbiamo mantenuto un occhio di riguardo per la “spiegabilità” dei modelli, intesa come la capacità di risalire alle cause di una predizione troppo bassa o troppo alta fornita dai modelli stessi. Sappiamo essere tanto importante addestrare i modelli nel modo corretto quanto avere la possibilità di imparare noi stessi dai modelli una volta sviluppati.
I risultati sono stati prodotti tramite l’utilizzo di modelli supervisionati addestrati su uno storico di prodotti e relativi test di qualità utilizzati come etichette. L’approccio supervisionato prevede l’addestramento di un modello fornendo in input allo stesso una porzione dei dati storici assieme agli output desiderati per quei dati. In questo modo il modello impara dagli esempi input-output forniti adattando i propri parametri interni. Uno degli ostacoli da superare per intraprendere questa strada è quella di associare i risultati dei test (etichette) ai dati che hanno partecipato alla produzione del prodotto testato.
Un passo oltre: on-line anomaly detection
Tempestività e precisione sono requisiti essenziali per l’intervento, da parte delle squadre di riparazione, durante situazioni impreviste come guasti, malfunzionamenti o fermi indesiderati degli impianti. A questo proposito abbiamo integrato il lavoro svolto per la previsione della qualità dell’acciaio con un meccanismo automatico di riconoscimento anomalie. Lo scopo è di fornire un sistema di alerting in near-real-time in grado di fornire un resoconto efficace riguardo la stabilità e lo stato del processo di produzione.
Tale meccanismo di riconoscimento anomalie può interagire con i modelli predittivi per la qualità del prodotto permettendo di correlare le anomalie riscontrate con la qualità del prodotto.
Questo approccio è stato condotto in modo non supervisionato, basandosi sull’autosimilarità delle fasi del processo durante la produzione in serie dei lavorati dell’acciaio. A differenza di un modello supervisionato, un modello non supervisionato non può contare sugli esempi input-output desiderati per adattare i propri parametri. Questa situazione si riscontra spesso nel riconoscimento di anomalie nei processi reali dato che non si ha una vera e propria definizione formale di anomalia sulla quale costruire gli esempi sopra citati.
Risulta quindi essenziale l’esperienza e la sensibilità degli esperti di dominio che sono in grado di validare e confrontare i risultati delle tecniche non supervisionate. Questo approccio human-in-the-loop ha permesso di migliorare notevolmente le prestazioni basate esclusivamente sulle proprietà statistiche delle variabili.
Le tecniche e le soluzioni di qualità predittiva sono fondamentali in tutti i campi in cui la lavorazione non prevede la possibilità di correzioni successive. Un esempio significativo è l’industria dell’acciaio. I modelli realizzati da Regesta Lab permettono di prevenire e riconoscere le anomalie nel materiale prodotto.