La trasformazione digitale del manifatturiero è stata avviata da alcuni anni ed è stata accelerata notevolmente dal Piano Industria 4.0, che ha dato un forte stimolo all’innovazione del settore. È con la pandemia però che anche i più scettici si sono resi conto di dover tenere il passo coi tempi: il monitoraggio e la manutenzione da remoto non erano più un lusso, ma una necessità. E, con l’attenuarsi delle limitazioni alla circolazione, le soluzioni messe in piedi in fase di emergenza sono state in alcuni casi potenziate, perché chi le ha adottate ha realizzato che potevano garantire una maggiore produttività e abbattere significativamente i costi, riducendo al minimo necessario gli spostamenti dei tecnici che forniscono l’assistenza, ma anche anticipando i guasti grazie a soluzioni di manutenzione predittiva. Queste ultime tengono sotto controllo tutti i parametri, e avvisano gli operatori quando alcuni di questi sono al di fuori dei range ottimali, segno di una possibile rottura. Intervenendo tempestivamente, è così possibile limitare di molto i fermi macchina, tutto a vantaggio dell’efficienza della produzione.
Abbiamo parlato dello smart monitoring qui, e in questa sede approfondiremo il concetto, andando ad analizzare le soluzioni SAP per abilitare lo smart monitoring e alcuni casi d’uso concreti.
IIoT, i parametri che contano
La manutenzione predittiva può essere abilitata sia sui macchinari più recenti, già dotati di tutta la sensoristica e la connettività necessari, sia su quelli più anziani, anche di decine di anni fa, ai quali vanno aggiunti degli economici sensori in grado di rilevare una serie di parametri chiave, che offrono indicazioni sul funzionamento dell’apparecchiatura. Quali parametri sono più importanti? In cima alla lista c’è il monitoraggio delle vibrazioni. Elevati livelli di vibrazione potrebbero essere causate da problemi ai cuscinetti, mentre piccole variazioni nei pattern delle vibrazioni potrebbero indicare un disallineamento di qualche componente.
Telecamere a infrarossi installate dei pressi delle macchine, invece, abilitano il real time temperature monitoring, consentendo di verificare in ogni istante le temperature di ogni singolo componente, così da individuare velocemente quelli che stanno iniziando a surriscaldarsi e che potrebbero quindi compromettere l’affidabilità dello strumento. Anche l’analisi dei suoni emessi dal macchinario è molto importante, dato che se affidata ad algoritmi di machine learning può segnalare il livello di usura di alcune parti.
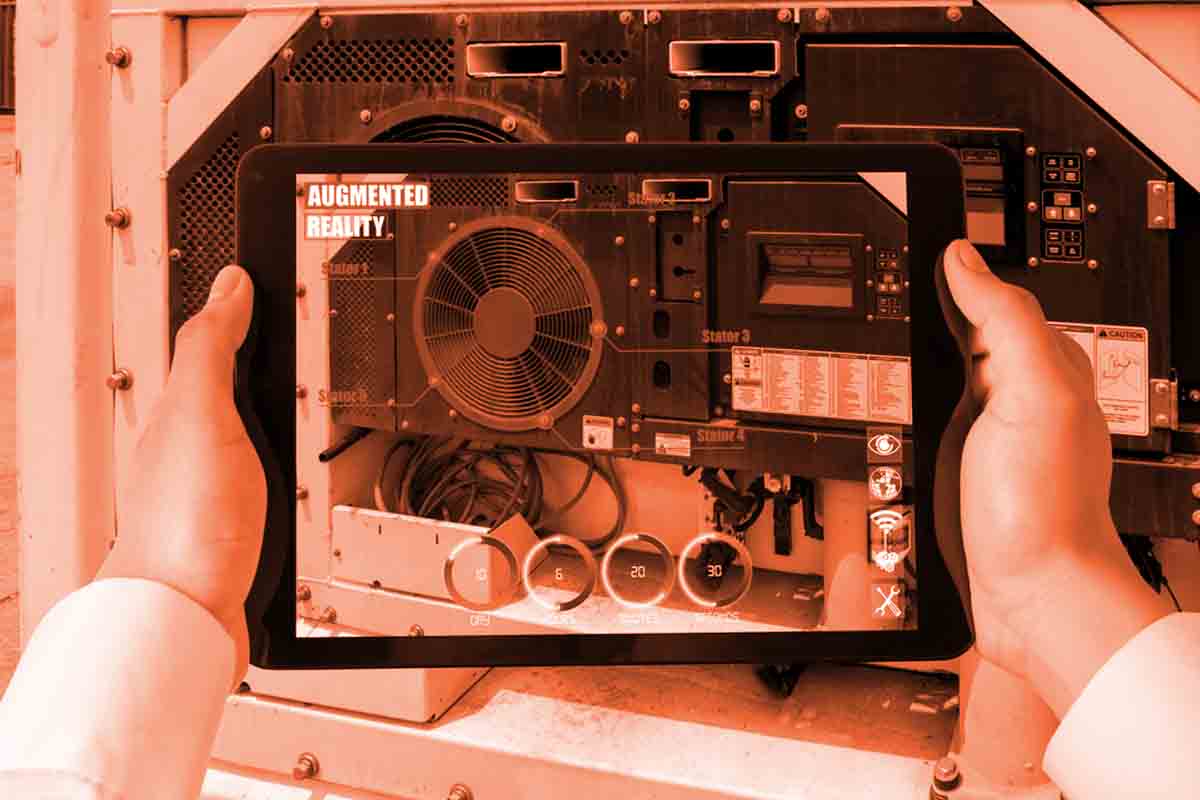
In maniera ben più efficace dell’orecchio umano, dato che i sensori sono in grado di acquisire anche frequenze ultrasoniche.
Quelli qui presentati sono solo alcuni esempi dei parametri chiave, ma non certo gli unici: l’analisi dei fluidi permette di verificare la corretta lubrificazione delle varie parti, mentre altri sensori permettono di identificare in anticipo corrosioni dei materiali, crepe nei macchinari, problemi ai circuiti elettrici.
Trenitalia migliora la manutenzione dei treni con SAP Predictive Maintenance and Service
La collaborazione fra SAP e Trenitalia va avanti da molti anni. Trenitalia è un’azienda che conta circa 30.000 mezzi fra locomotive, treni elettrici, veicoli per trasporto di passeggeri e merci e ogni giorno sono attivi circa 8.000 dei suoi treni sulla rete ferroviaria. Una flotta non facile da tenere in efficienza, e per ottimizzare le operazioni di manutenzione l’azienda ha adottato le soluzioni SAP. Nello specifico, SAP Predictive Maintenance and Service permette di analizzare i dati dei sensori IoT installati a bordo dei mezzi e monitorare lo status dei veicoli da remoto. Il sistema di analisi predittiva basato su SAP HANA infine elabora questa enorme mole di informazioni tramite algoritmi di machine learning, così da verificare eventuali problemi prima che si presentino e pianificare in maniera più efficace la manutenzione, così da limitare il più possibile i tempi di inattività non pianificati e abbattere i costi di manutenzione dall’8% al 10%.
In che maniera? I dati acquisiti (parliamo 5.000 valori registrati al secondo, circa 450 miliardi di valori quotidianamente) hanno permesso col tempo di comprendere meglio quanti cicli di apertura chiusura potevano sopportare i portelli prima di esibire malfunzionamenti, ma anche la durata dei freni. Precedentemente ci si basava su una stima chilometrica, ma le soluzioni SAP hanno aiutato l’azienda a stimare con più precisione l’usura misurando il calore dissipato durante la frenata. L’adozione della soluzione di Smart Monitoring ha permesso anche di identificare correlazioni che sarebbero state molto difficili da scovare, come il differente rendimento di alcuni tipi di batteria su treni diversi.
Il passo successivo al real time monitoring: il digital twin
Acquisire dati in tempo reale permette di abilitare la manutenzione predittiva e il monitoraggio da remoto, ma è anche possibile estendere ulteriormente questo concetto, arrivando a realizzare un gemello digital, un digital twin, di uno specifico asset, o di un’intera fabbrica. Il vantaggio è che si avrà una riproduzione digitale identica in tutto all’asset originale, anche perché i dati che alimentano questo gemello sono quelli acquisiti in tempo reale dal macchinario. A cosa servono i digital twin? Gli scenari di utilizzo sono molteplici, ma il vantaggio principale è che permettono di simulare scenari alternativi senza toccare gli strumenti produttivi, così da migliorare l’efficienza dei processi, ridurre i consumi energetici, ottimizzare in generale la produzione e la distribuzione.
Un esempio arriva dal colosso Unilever, che nel 2019 ha lanciato un progetto pilota su un suo stabilimento produttivo (sapone, nello specifico), con l’intenzione di estenderlo a tutte le 300 fabbriche. Il risultato è stato positivo e l’adozione del digital twin ha consentito allo stabilimento di incrementare la produttività e allo stesso tempo ridurre i consumi energetici. Nello specifico, Unilever sostiene che l’adozione in un solo stabilimento ha portato a risparmi per 2,8 milioni di dollari.
Lo smart monitoring è una parte fondamentale di qualsiasi iniziativa di trasformazione digitale. Raccogliendo dati e monitorando i consumi, è possibile contenere i costi e comprendere meglio come l’azienda sfrutta le risorse e utilizza la tecnologia.
Contattaci per ricevere maggiori informazioni e prenotare la tua consulenza gratuita.